加工治具一体化による脱着回数削減で作業効率の改善事例
御困り事内容 | 工程改善 | 業界 | 自動車 |
---|---|---|---|
用途 | エンジン部品 | 提案効果 | 工数削減・効率化 |
Before
この事例は、エンジン用のバランスシャフトへの工程改善事例の一つです。
製品が複雑な形状であるため、専用治具を用いて加工を行っていました。しかし、工程ごとに加工治具を製作していたため、段取り替えが都度発生し、工数アップの要因となっていました。
製品が複雑な形状であるため、専用治具を用いて加工を行っていました。しかし、工程ごとに加工治具を製作していたため、段取り替えが都度発生し、工数アップの要因となっていました。
After
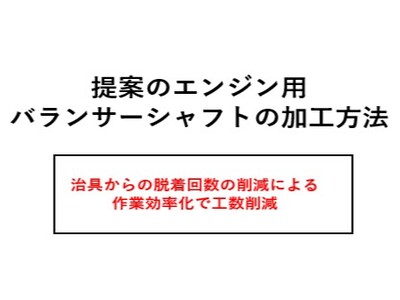
そこで、加工治具を集約し、同じ治具で複数の工程の加工を可能にしたことで、治具からの脱着回数の削減による作業効率の向上を提案しました。また、ワンチャックでの加工となるため、基準面に対しての加工精度向上が実現でき、加工における工数の低減ならびに、仕上がり品質の向上を実現しました。
POINT
本事例では、社内の工程改善によるコストメリット提案についてご紹介をいたしました。
複雑な製品の加工においては、加工治具を用いることで品質の安定性を生むことに繋がりますが、治具を複数個使用することによる治具脱着時間のアップも充分に考慮しなければなりません。そこで、今回の様に多工程にわたる加工品の場合においても治具の数を減らし、より合理的な加工工程を組むことで製品の精度向上に寄与することができます。
部品の仕様が決まった製品で、工程における効率化や、品質向上についてご検討の方は当サイト量産シャフト加工VA・VEセンターを運営する東陽製作所にお問い合わせください。
複雑な製品の加工においては、加工治具を用いることで品質の安定性を生むことに繋がりますが、治具を複数個使用することによる治具脱着時間のアップも充分に考慮しなければなりません。そこで、今回の様に多工程にわたる加工品の場合においても治具の数を減らし、より合理的な加工工程を組むことで製品の精度向上に寄与することができます。
部品の仕様が決まった製品で、工程における効率化や、品質向上についてご検討の方は当サイト量産シャフト加工VA・VEセンターを運営する東陽製作所にお問い合わせください。
VA・VE事例一覧

スタブシャフトの切削加工における工具のコストダウン事例
御困り事内容: | コストの削減 |
---|---|
用途: | ドライブトレイン部品 |
業界: | 自動車 |
提案効果: | 工具費の低減 |
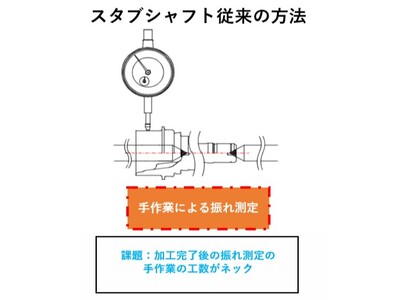
設備の2ライン持ちによる1個当たり工数低減事例
御困り事内容: | 工数削減 |
---|---|
用途: | ドライブトレイン部品 |
業界: | 自動車 |
提案効果: | 工数削減・効率化 |
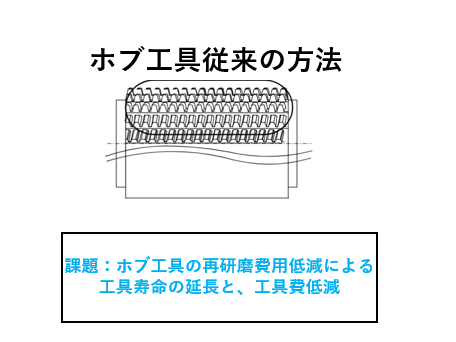
ホブの工具寿命を延ばすことによる工具コストダウン事例
御困り事内容: | コストの削減 |
---|---|
用途: | ドライブトレイン部品 |
業界: | 自動車 |
提案効果: | 工具費の低減 |
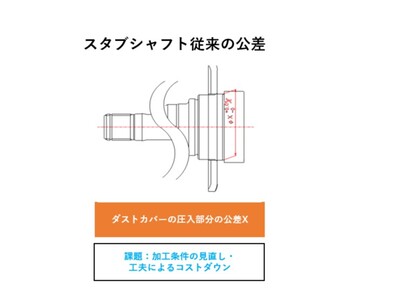
スタブシャフトの加工不良率低減に伴うコストダウン事例
御困り事内容: | 加工不良率の改善 |
---|---|
用途: | ドライブトレイン部品 |
業界: | 自動車 |
提案効果: | 不良率の低減 |
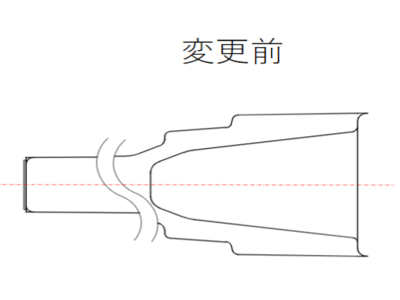
粗材の形状変更による原価低減・軽量化の提案事例
御困り事内容: | コストの削減 |
---|---|
用途: | ドライブトレイン部品 |
業界: | 自動車 |
提案効果: | 軽量化 |
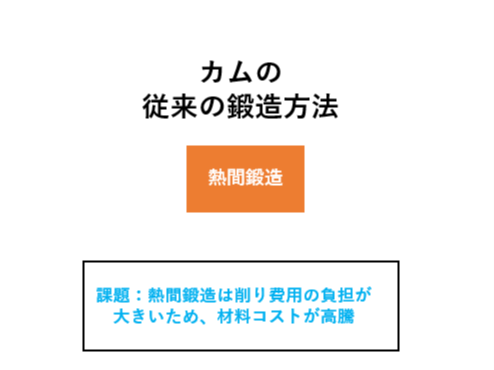
自動車用ステアリング部品の一つであるカムの鍛造工法転換によるコストダウン事例
御困り事内容: | 工法転換 |
---|---|
用途: | ステアリング部品 |
業界: | 自動車 |
提案効果: | 材料歩留まり向上 |
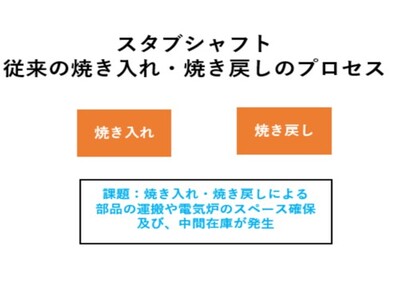
焼入れ・焼戻しの工法変更による工程集約事例
御困り事内容: | 工程改善 |
---|---|
用途: | ドライブトレイン部品 |
業界: | 自動車 |
提案効果: | 工数削減・効率化 |
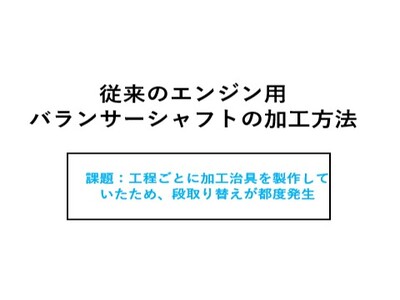
加工治具一体化による脱着回数削減で作業効率の改善事例
御困り事内容: | 工程改善 |
---|---|
用途: | エンジン部品 |
業界: | 自動車 |
提案効果: | 工数削減・効率化 |
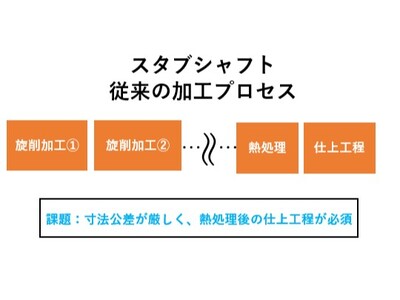
寸法公差緩和による仕上げ工程廃止で作業効率向上の事例・製造リードタイム短縮事例
御困り事内容: | 工程改善 |
---|---|
用途: | ドライブトレイン部品 |
業界: | 自動車 |
提案効果: | 工数削減・効率化 |
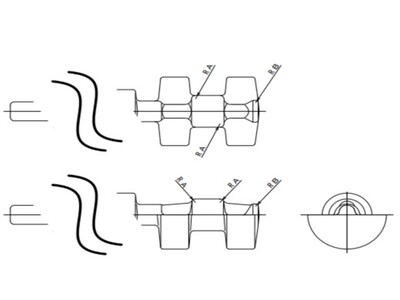
バランスシャフト加工後のバリ取り工数の削減による製造リードタイム短縮事例
御困り事内容: | 加工後のバリ取り工数の削減 |
---|---|
用途: | エンジン部品 |
業界: | 自動車 |
提案効果: | 工数削減・効率化 |
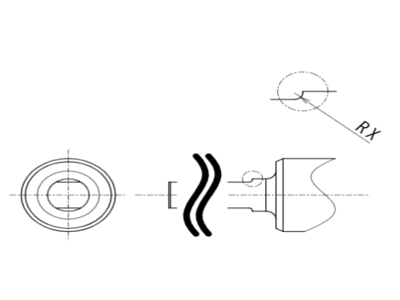
バランスシャフト量産加工の工具費コストダウン事例
御困り事内容: | コストの削減 |
---|---|
用途: | エンジン部品 |
業界: | 自動車 |
提案効果: | 工具費の低減 |
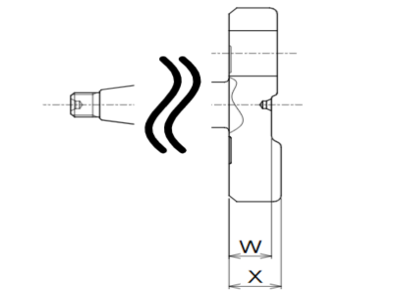
農機用量産部品における寸法変更及び、加工レスによるコストダウン事例
御困り事内容: | 加工レス化による加工費の削減 |
---|---|
用途: | エンジン部品 |
業界: | 農機 |
提案効果: | 工数削減・効率化 |