クランクシャフトの寸法変更によるコストダウン事例
御困り事内容 | 工具変更による加工費削減 | 業界 | 農機 |
---|---|---|---|
用途 | エンジン部品 | 提案効果 | 工数削減・効率化 |
Before
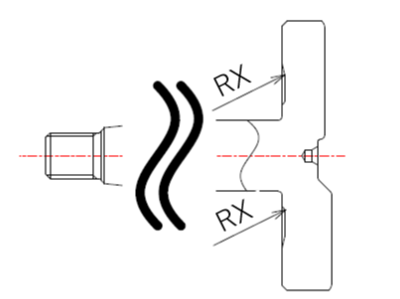
この事例は、粗材の寸法変更並びに工具変更(ノーズR変更)により加工費の低減を図ったVAVE提案・カイゼン事例になります。
シャフトの量産品の加工コストをもう少し下げられないかということで、当社にご相談いただきました。
シャフトの量産品の加工コストをもう少し下げられないかということで、当社にご相談いただきました。
After
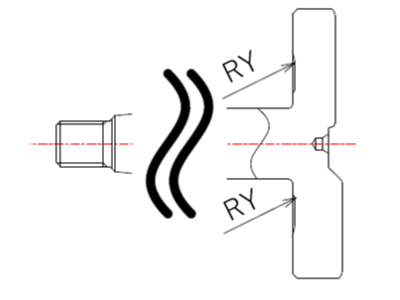
そこで当社は、お客様とご相談したうえでワークの該当部位の寸法をRXからRYへと緩和、それに合わせて旋盤加工に用いるチップのノーズRを大きくしました。これにより切削工具の持ちが良くなるため切削工具費が大幅に下がり、年に換算するとおよそ数万円のコストダウン効果をもたらすことができました。
POINT
本事例のポイントは、寸法・形状の緩和によりチップのノーズRを大きくしたことで、切削工具コストの低減を実現した点にあります。
一般に、ノーズRはチップの先端に施されているR処理のことを指しますが、このノーズRが小さいと切削面の抵抗が抑えられるために切粉の排出性が良好である一方、工具寿命は短くなります。他方、ノーズRが大きくなると欠けにくくなり、持ちが良くなります。
当サイト量産シャフト加工VA・VEセンターを運営する東陽製作所では、本事例のような切削工具の工夫をはじめとする様々なVAVE提案・カイゼンに取り組んでいます。まずはお気軽にご相談ください。
一般に、ノーズRはチップの先端に施されているR処理のことを指しますが、このノーズRが小さいと切削面の抵抗が抑えられるために切粉の排出性が良好である一方、工具寿命は短くなります。他方、ノーズRが大きくなると欠けにくくなり、持ちが良くなります。
当サイト量産シャフト加工VA・VEセンターを運営する東陽製作所では、本事例のような切削工具の工夫をはじめとする様々なVAVE提案・カイゼンに取り組んでいます。まずはお気軽にご相談ください。
VA・VE事例一覧

スタブシャフトの切削加工における工具のコストダウン事例
御困り事内容: | コストの削減 |
---|---|
用途: | ドライブトレイン部品 |
業界: | 自動車 |
提案効果: | 工具費の低減 |
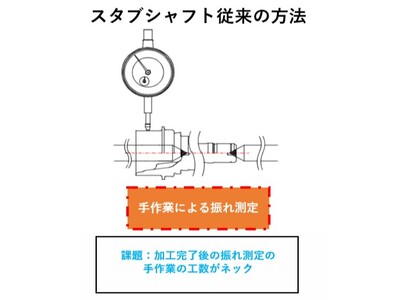
設備の2ライン持ちによる1個当たり工数低減事例
御困り事内容: | 工数削減 |
---|---|
用途: | ドライブトレイン部品 |
業界: | 自動車 |
提案効果: | 工数削減・効率化 |
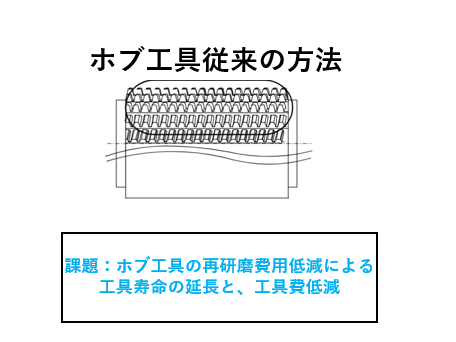
ホブの工具寿命を延ばすことによる工具コストダウン事例
御困り事内容: | コストの削減 |
---|---|
用途: | ドライブトレイン部品 |
業界: | 自動車 |
提案効果: | 工具費の低減 |
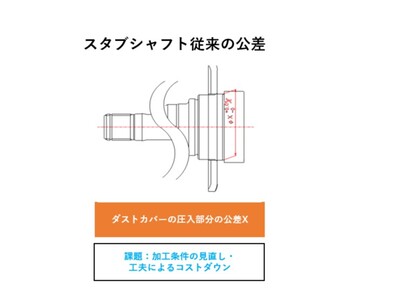
スタブシャフトの加工不良率低減に伴うコストダウン事例
御困り事内容: | 加工不良率の改善 |
---|---|
用途: | ドライブトレイン部品 |
業界: | 自動車 |
提案効果: | 不良率の低減 |
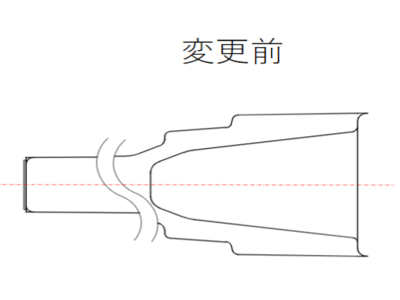
粗材の形状変更による原価低減・軽量化の提案事例
御困り事内容: | コストの削減 |
---|---|
用途: | ドライブトレイン部品 |
業界: | 自動車 |
提案効果: | 軽量化 |
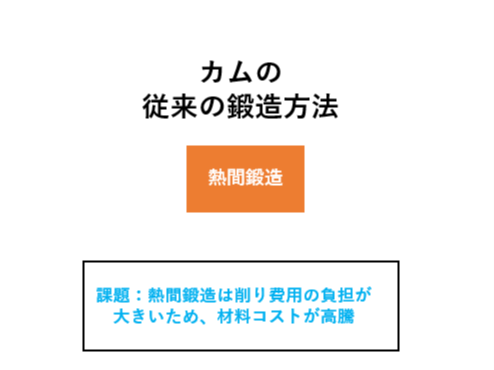
自動車用ステアリング部品の一つであるカムの鍛造工法転換によるコストダウン事例
御困り事内容: | 工法転換 |
---|---|
用途: | ステアリング部品 |
業界: | 自動車 |
提案効果: | 材料歩留まり向上 |
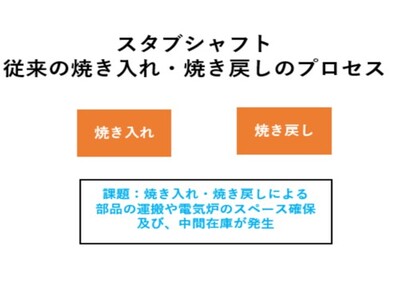
焼入れ・焼戻しの工法変更による工程集約事例
御困り事内容: | 工程改善 |
---|---|
用途: | ドライブトレイン部品 |
業界: | 自動車 |
提案効果: | 工数削減・効率化 |
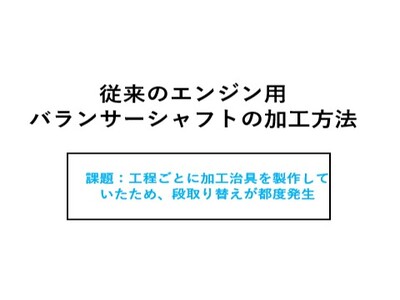
加工治具一体化による脱着回数削減で作業効率の改善事例
御困り事内容: | 工程改善 |
---|---|
用途: | エンジン部品 |
業界: | 自動車 |
提案効果: | 工数削減・効率化 |
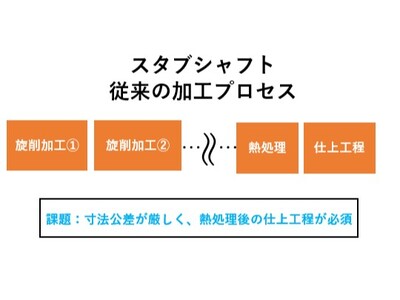
寸法公差緩和による仕上げ工程廃止で作業効率向上の事例・製造リードタイム短縮事例
御困り事内容: | 工程改善 |
---|---|
用途: | ドライブトレイン部品 |
業界: | 自動車 |
提案効果: | 工数削減・効率化 |
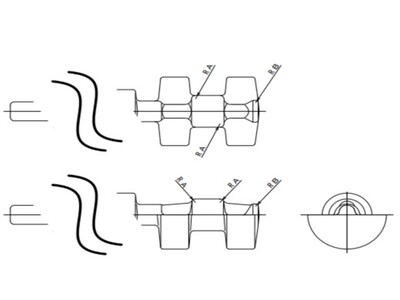
バランスシャフト加工後のバリ取り工数の削減による製造リードタイム短縮事例
御困り事内容: | 加工後のバリ取り工数の削減 |
---|---|
用途: | エンジン部品 |
業界: | 自動車 |
提案効果: | 工数削減・効率化 |
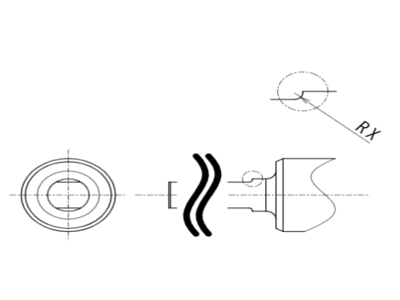
バランスシャフト量産加工の工具費コストダウン事例
御困り事内容: | コストの削減 |
---|---|
用途: | エンジン部品 |
業界: | 自動車 |
提案効果: | 工具費の低減 |
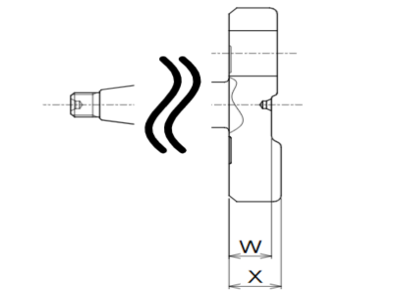
農機用量産部品における寸法変更及び、加工レスによるコストダウン事例
御困り事内容: | 加工レス化による加工費の削減 |
---|---|
用途: | エンジン部品 |
業界: | 農機 |
提案効果: | 工数削減・効率化 |